May 02, 2019 Project of the Week
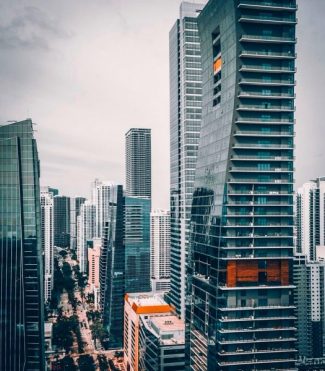
Project Name: Panorama Tower
Company Name: Siemens
Project Location: Miami, Florida United States
Project Information/Details: Siemens is working with Florida East Coast Realty (FECR) to implement smart building solutions in Miami’s 85-story Panorama Tower. Technologies used throughout the residential, commercial, and retail space unify disparate fire and life safety systems, signal third-party elevator systems to restrict end user access by floor, and monitor and control more than 1,500 pieces of mechanical equipment throughout the complex. The solutions were installed with flexibility and future-proofing in mind but also to make it easier for occupants to go from one part of the building to another. Located in the up-and-coming Brickell neighborhood, Panorama Tower is currently the tallest building on the East Coast, south of Manhattan. In addition to apartments, the building includes offices, restaurants, and shops, and connects to an adjacent 19-floor hotel. The entire space measures 2.7 million square feet, with occupants from both buildings able to access the Tower’s garage and pool. “The Panorama Tower project was seven years in the making and, as such, building systems originally specified had to be modified at times, to meet updated codes and changing occupant needs,” recalls Dean Warhaft, Chief Development Officer for FECR. “Siemens kept pace with our requirements and even anticipated future needs.” “Integration was key to helping bring our customer’s vision of a vertical city to life,” notes Dave Hopping, President and CEO of Siemens Smart Infrastructure USA. “Our project team was able to figure out how to make several already-installed third-party systems in the Tower and neighboring hotel work cohesively with our smart building solutions. For tenants and visitors, this means being able to easily go from one part of the building to another while also being comfortable and safe.” Siemens’ FireFinder® XLS system with global voice network acts as a comprehensive fire command center that controls fire alarm, smoke control, and containment technologies, all from a single platform. The fire panel also integrates a disparate carbon monoxide system from the garage. Tower security is monitored by Siemens cameras and controlled by the SiPass® integrated access control system, which is compatible with third-party elevator control systems. The integrated systems allow occupants access to select floors, based on building credentials assigned to the key card and registered by the elevator system. For instance, hotel users can make use of the gym or pool, located on the residential Tower. Finally, more than 1,500 pieces of mechanical equipment located throughout the Tower are monitored and controlled using Siemens’ building automation. And for added security and reliability, Siemens recommended that building automation and security each have their own dedicated high-speed fiber optic network, separate from the residential network. “Siemens helped create the seamless tenant experience we wanted for all of our building occupants,” concludes FECR’s Warhaft.
April 23, 2019 Project of the Week
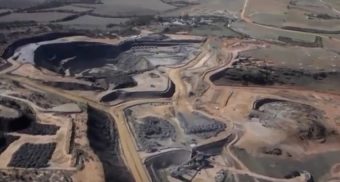
Project Name: Hillgrove Kanmantoo Mine
Company Name: AGL
Project Location: Adelaide Hills, Australia
Project Information/Details: Australian energy generator AGL has secured the right to develop, own and operate a 250-megawatt pumped hydro energy storage project at Hillgrove Resources Limited’s Kanmantoo copper mine in the Adelaide Hills region of South Australia. The contract allows AGL to transform the Kanmantoo open pit mine into a pumped hydro facility while Hillgrove will retain processing and mining rights outside the Giant Pit. AGL’s Executive General Manager of Wholesale Markets Richard Wrightson said the signing of binding agreements was the start of a multiple stage process to progress the project, including the lodgement of a development application in 2020. “If we proceed and the project is approved, it would be an important addition to our technology mix in South Australia, where we have significant wind and thermal generation,” he said. “It would help us to meet the changing needs of the South Australian energy market, in which energy storage assets are likely to be needed to provide dispatchable capacity as renewables generation increases over coming years. “If all approvals are received, we expect the project to be complete and operating by 2024.” AGL would buy the land required for the project from Hillgrove shortly after a final investment decision, which is expected to be made following the completion of processing at Kanmantoo as early as this year. The Hillgrove Kanmantoo mine sits between Mount Barker and Murray Bridge, about 50km east of Adelaide and has been back in operation since 2010 following initial production from 1970 to 1976. Hillgrove CEO Steve McClare said the project would benefit the state, which already had a strong reputation for renewable energy and successful storage projects. “The trust, support and growth of the community around Kanmantoo has been deeply valued by us and we are pleased to have found a solution that will continue to bring economic benefits, not just to the local community, but to South Australia more broadly,” he said. South Australian Chamber of Mines and Energy (SACOME) Chief Executive Officer Rebecca Knol said Hillgrove should be commended for its creative and forward-thinking approach to post open pit mining. “This solution is one that takes advantage of the unique topography & geology and will provide an ongoing economic contribution to South Australia,” she said. “This is a company that had gone above and beyond legal requirements throughout the life of the mine and again they are raising the bar post closure. “Hillgrove provides a real example of the positive contributions mining companies can make to the communities in which they operate.” South Australia leads the nation in the uptake of wind energy and roof-top solar with renewable sources accounting for more than 50 per cent of the electricity generated in the state. It is also the home to ‘world’s biggest battery’, which was famously installed by Elon Musk’s company Tesla at Neoen’s Hornsdale wind farm in the state’s Mid North in December 2017.
April 16, 2019 Project of the Week
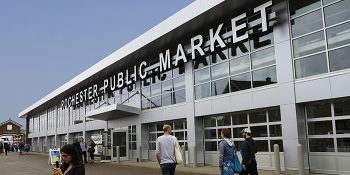
Project Name: Rochester’s Public Market Wintershed
Company Name: T.Y. Lin International
Project Location: Rochester, New York United States
Project Information/Details: The City of Rochester, New York, initially enlisted T.Y. Lin International (TYLI) to prepare the Master Plan for the comprehensive renovation and expansion of Rochester’s Public Market Wintershed facility. The Public Market is a year-round bustle of activity on nine acres in the heart of the city. It enjoys national acclaim; it was voted “America’s Favorite Farmer’s Market,” has operated on the same site since 1905, and attracts more than 1.5 million shoppers each year. The Market was comprised of the market office and public restroom facility, Shed A, Shed C, and the Wintershed facility, a 10,457-square-foot indoor area of vendor stalls. The Wintershed facility did not adequately meet vendor needs, public usage, or current building code. The project vision was to increase the number of vendors, create multiple aisles and kiosks aimed to improve customer traffic, enable varied storefront capability for indoor/outdoor use as the seasons dictate, and incorporate code-approved restroom, mechanical, electrical, and plumbing system improvements. TYLI secured one of the foremost public market experts in the county and led the renovation effort. TYLI’s initial contract covered the project from program development through schematic design phase. Responsibilities included a condition survey and report/market analysis of the existing Wintershed facility; site evaluation, survey, and plan development of the site; preparation of State Environmental Quality Review (SEQR) documentation; and assistance in obtaining environmental approvals. Once the Master Plan was complete, the City of Rochester enlisted TYLI to implement its award-winning efforts. The first step was to develop a new linear, open Shed D and replace the existing Wintershed with a new, enclosed, year-round use building (Shed B). Shed B is the first completely new building at the Market in more than 40 years. It presents a clean, modern architectural style that complements and enhances the collection of historic and utilitarian buildings of the Market complex. Project Highlights: TYLI developed Shed D to match the visual aesthetic of the adjacent outdoor vendor sheds. Shed B provides flexible space for an assortment of vendors. It has utility support for wholesale meat and fish vendors, as well as prepared food operations. Innovative operable glass doors allow the vendor activity to extend out into the Market Plaza in good weather. The new building houses expanded, fully accessible restroom facilities to serve the Market as a whole. The design carefully incorporated phasing considerations and detailed planning for construction access and activity, which allowed the Market to remain operational and retain vendors throughout the construction process. TYLI provided full, multi-disciplinary services, including civil, structural, architectural, and mechanical, electrical, and plumbing (MEP) design. TYLI also provided construction administration services, which included submittal review, RFI (requests for information) response, status meetings, pay application review, and punch list inspection. Awards Mayor’s Award, 2018 American Institute of Architects (AIA) Rochester Chapter Design Excellence Award, 2018 American Institute of Architects (AIA) Rochester Chapter Design Excellence Award, 2013 American Institute of Architects (AIA) Rochester Chapter Planning Excellence Award for Best Practice, 2012 American Planning Association (APA) New York Upstate Chapter