Hot-in-Place Asphalt Recycling Yields Benefits for Road Rehabilitation

Rehabilitating asphalt-paved roads has been growing in popularity thanks to the availability of more cost-effective solutions. One industry-leading method is hot-in-place recycling (HIR), an onsite method for deteriorated blacktop pavement rehabilitation. According to the Asphalt Recycling & Reclaiming Association, the three most-common HIR processes are surface recycling, surface repaving and surface remixing.
1. Surface recycling starts with recycling 1 to 2 inches of the asphalt, in ½-inch increments, which then is re-applied and compacted. Next, a thin overlay of new hot-mix asphalt or another thin surface treatment is placed on top of the recycled layer.
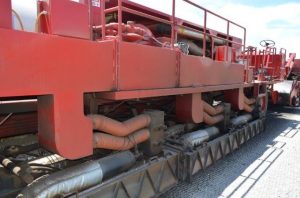
The existing pavement is initially softened with the first application of heat applied by the preheater conveying vehicle in advance of the main repaver.
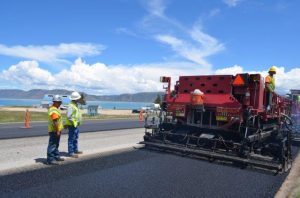
The recycling screed gathers and lays the recycled material in advance of the main paving screed.
2. Surface repaving involves recycling the top 1 to 2 inches of pavement and placing a new hot-mix asphalt layer atop the recycled layer in a single pass of the equipment, followed by compaction.
3. Surface remixing blends old and new asphalt with additives and additional aggregates. The new mixture is applied, and the roadway is compacted. A final wearing surface can be applied separately, if necessary.
Numerous Benefits
HIR uses up to 35 percent less energy than conventional paving methods; requires up to 50 percent less asphalt cement than conventional equivalent methods; and minimizes lane closures, sparing motorists the risks of driving on uneven, oily surfaces and the dangers of loose rocks and other construction debris.
By using less energy and emitting fewer greenhouse gases than other pavement methods, HIR also can help meet sustainability requirements. Because the repaving method is completed in a single pass, it saves time and taxpayer dollars.
Despite HIR’s benefits, however, the process hasn’t yet gained widespread usage with state departments of transportation, primarily due to issues with HIR’s durability on certain projects. When these projects were reviewed, however, the problem frequently was a failure to perform a thorough surface evaluation in advance to determine whether HIR was the proper solution.
Evaluation, Materials Make a Difference
Prior to the start of a repaving project, various types of pavement distresses should be evaluated, including the following:
• Surface defects
• Deformations
• Load-associated cracking
• Non-load-associated cracking
• Combined cracking
• Base/subgrade deficiencies
• Roughness
• Miscellaneous other distresses (e.g., levels of traffic, drainage, rural vs. urban area, etc.)
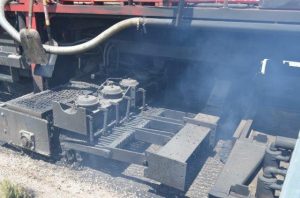
Carbide-tipped teeth cut the heated, softened pavement in a level plane without breaking apart the individual aggregates in the existing pavement.
The presence of any of these factors doesn’t automatically mean the pavement isn’t suited to repaving—in most cases it still will be appropriate.
According to John Rathbun with Lawrence, Kan.-based Cutler Repaving Inc., the most common reason for rejecting an HIR candidate is that the base material is too deteriorated.
“We are trying to correct problems in the top 1 to 2 inches of pavement,” notes Rathbun. “If the condition of the underlying roadway is too disintegrated, then the project is not suitable for HIR.”
The selection of the asphalt recycling agent should be approved by the project engineer prior to the project’s start. Possible materials include hot-mix asphalt, asphalt rubber, asphalt friction course, asphalt rubber friction course, warm mix or stone matrix asphalt. These materials can be placed on top of the recycled layer in simultaneous operation with a single piece of equipment. After the client selects the surface type of HMA, a mix design should be submitted and approved prior to use.
The Keys to HIR
To ensure the reconditioned pavement will not deteriorate prematurely, it’s essential to first evaluate the existing pavement’s constituent materials and properties. Variability within the pavement materials, gradation or asphalt content can alter the properties of the applied HIR pavement. If not accounted for during mix design, this variability may affect the quality of the product and impact performance.
Recycling the pavement in place means there’s no need to remove material and haul it away, saving time and material. After HIR has been deemed compatible as a rehabilitation method with the current surface, the existing asphalt pavement is assessed to verify the thickness, asphalt content, viscosity and penetration of the existing materials. After its properties are determined, the recycled materials are mixed and laid down to form a leveling course. A layer of fresh hot-mix asphalt then is applied and the roadway compacted.
Recent advances and innovations to the HIR process are increasing its efficiency and value, including the hot-in-place single-pass process known as repaving, which completes the road rehab in one step, saving time and money. Whichever process is employed, proper evaluation and testing of the existing pavement are the keys to maximizing the performance and value of HIR.
Benefits of Recycling Asphalt
• Uses less energy and emits fewer greenhouse gases than other rehabilitation methods.
• HIR can help meet sustainability requirements.
• HIR can use up to 50 percent less asphalt cement than conventional equivalent methods.
• HIR minimizes lane closures, and motorists are spared the risk of driving on uneven, oily surfaces as well as the dangers of flying rocks and construction materials.
• Lower energy consumption is important for cost savings and resource conservation. In a study conducted by the Federal Highway Administration, HIR was found to consume up to 35 percent less energy than conventional paving methods.
• Allows for more overlays before requiring milling or replacement on future rehabilitation. This process typically raises the roadway 1 inch versus 2-3 inches for a conventional overlay.
How HIR Is Performed
The single-pass method of surface repaving means the work is performed with a single machine that heats, scarifies, recycles and spreads new asphalt hot mix, all in one continuous pass. Additional preheaters may be utilized to achieve specified depth and temperature. This process is defined as “repaving” in the Basic Asphalt Recycling Manual published by the Asphalt Recycling & Reclaiming Association.
The aforementioned Cutler Repaving uses a six-step process:
1. Heating the existing pavement.
2. Scarifying the heated, softened pavement to a 1-inch depth.
3. Applying a recycling agent to the scarified material to restore viscosity of the aged asphalt.
4. Mixing and laying the recycled material to form a leveling course.
5. Applying the virgin hot mix while the temperature of the recycled mix is still 225 degrees Fahrenheit.
6. Final compaction.
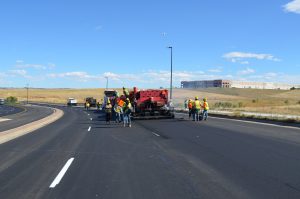
A hallmark of a Cutler pavement is the heated, monolithic joints between adjoining mats that provide increased joint density.
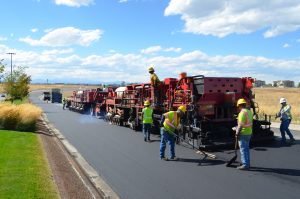
The existing pavement is recycled and resurfaced in a single pass of the Cutler Repaving equipment, thereby minimizing traffic delays.
Although a preheater is used in advance of the repaver, Cutler’s single-pass process ensures a thermal, monolithic bond is achieved, because the repaver recycles and lays the final wearing surface simultaneously. The unique process minimizes traffic delays and offers improved conditions for motorist safety and convenience.
The specified hot-mix asphalt is delivered to the repaver and deposited in the front receiving hopper, where it’s conveyed the length of the repaver by a drag-slat conveyor to the paving screed, where it’s laid and compacted. This work shouldn’t be done when it’s raining or if there’s a threat of rain. The ambient temperature should be at least 50 degrees Fahrenheit and rising. If the temperature reaches 55 degrees and then starts cooling, the application should cease.
Although HIR isn’t a “one size fits all” solution for asphalt-paved-road rehabilitation, a proven evaluation and testing process as well as proper materials selection limits uncertainty and can reduce costs for HIR deployment.
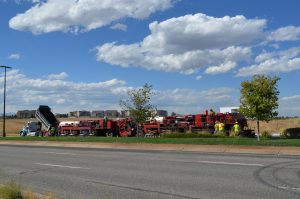
New hot mix is delivered to the Cutler preheater conveying vehicle, allowing the existing pavement to be recycled in a single pass of the equipment.
Mark Wells, P.E., PMP, is a senior project materials engineer in Terracon’s Houston office; email: [email protected]
About Mark Wells
Mark Wells, P.E., PMP, is a senior project materials engineer in Terracon’s Houston office; email: [email protected].